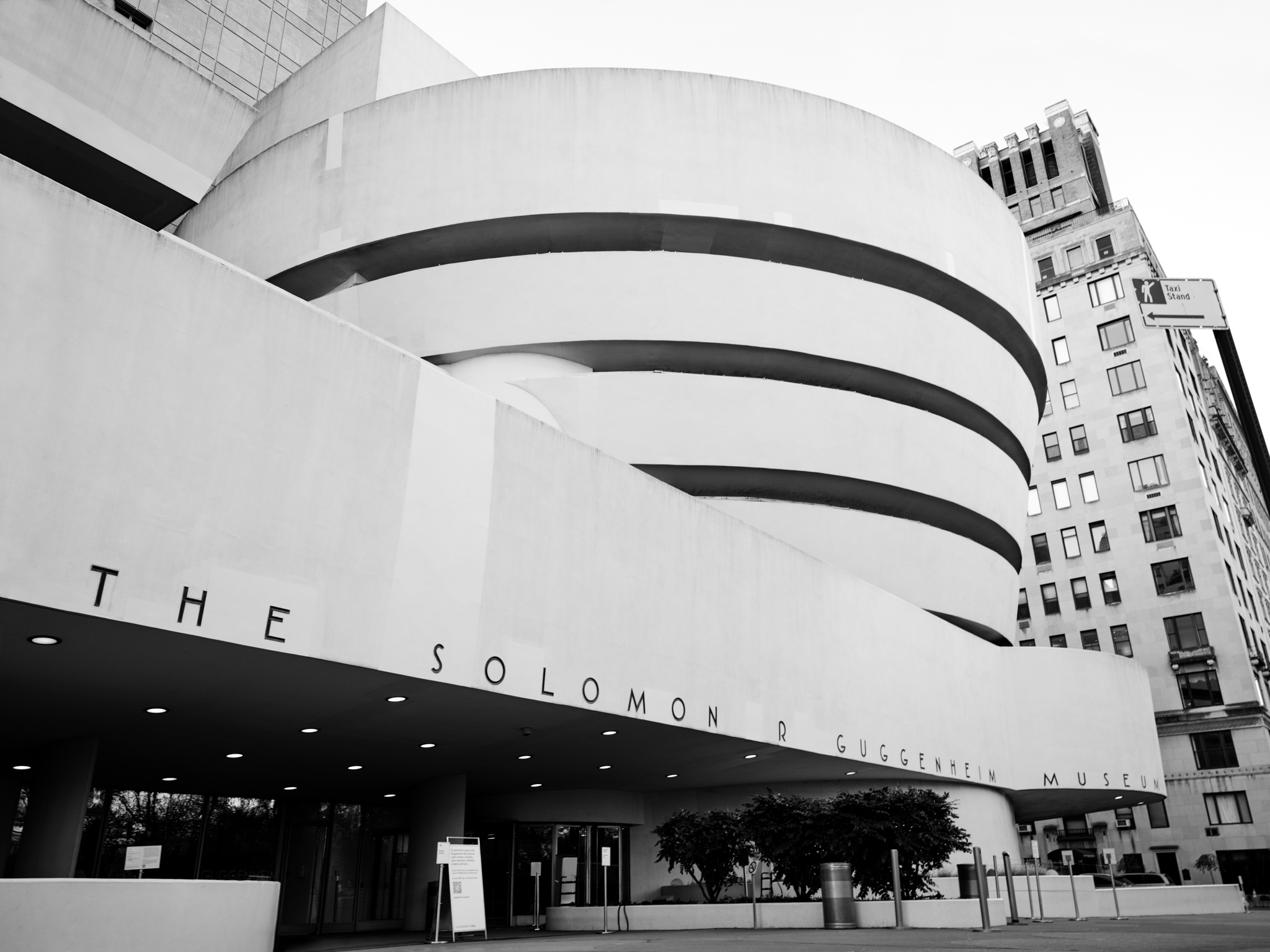
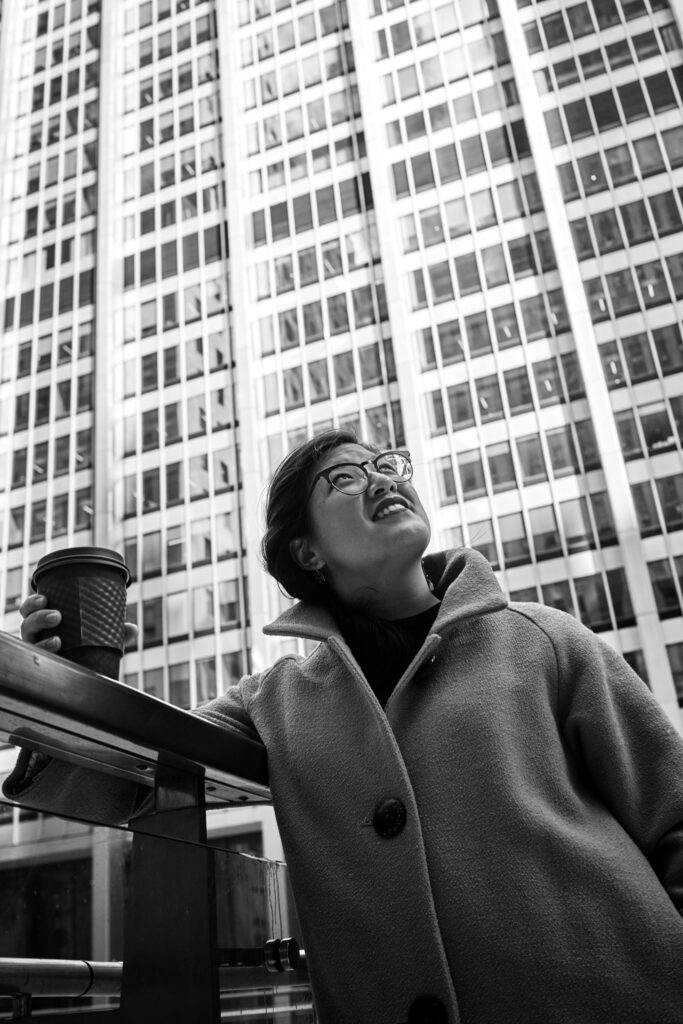
Extracting stone from the earth to build with it is a tale as old as time.
In the past, we would build with whatever we had on hand – sticks, mud, hay, etc. If you’ve ever played the popular board game the Settlers of Cattan, you’ll be familiar with the concept of resources as direct means for building and for establishing’s one’s presence. If your building stands the test of time and attack (of mother nature or of the human sort), your dominance was asserted. So, from sticks, mud, hay, we graduated to stone (before industrial firing made modern brick masonry an accessible and popular construction material). With stone, we also could build taller too. A great example is the original skyscrapers, of medieval Italy, where feuding influential families would assert their dominance over each other with taller and taller towers – which sometimes resulted in the dumping of waste and other unpleasant things (ew) from the taller tower to the shorter tower.
So, this is why humans have generally congregated in resource rich areas. Of the earth, gifts from mother nature enable us to survive and maybe thrive. But, sometimes we get a bit greedy.
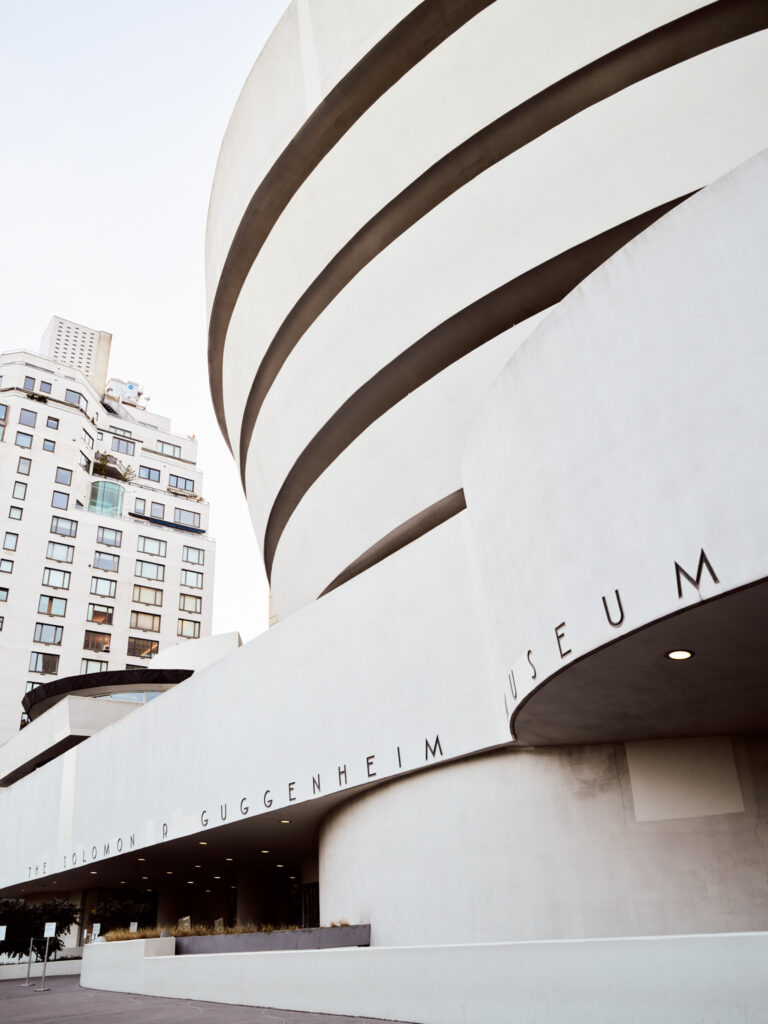
The original design for the Guggenheim Museum of the architect Frank Lloyd Wright included pink marble panels to cover the concrete round geometry, which was inspired by Native American Pottery, achieved with the cutting edge technology called gunite. We now know gunite as the predecessor to shotcrete, which is as it sounds – concrete shot out of a hose unto rebar, contained with form work to create non linear and expansive structures. Not all concrete can be used in this process. Generally, while concrete is extraordinarily damaging to the environment, shotcrete can be even worse because of the additional ingredients required to keep it liquid enough to go through a hose. Concrete is made up of cement, aggregate, sand, and water; the cement is like egg for cake batter – it holds the cake together. However, while there isn’t much of it in the mix, it is disproportionately responsible for contributing to pollution. Much like egg alternatives such as flax seed, apple sauce, or egg replacement for those with allergies, aversions, or vegan diets, you can change up the mix itself, but you’ve got to work at perfecting that recipe to literally see what sticks, concretely.
Concrete is of the earth, but a product of more human processing than of mother nature. That processing results in pollution, global climate change, and global warming, which we in the industry quantify as embodied carbon (EC). EC refers to carbon dioxide arising from the manufacturing, transportation, installation, maintenance, and disposal of building materials.
EC is different from operational carbon, which are emissions that result from energy use during the lifetime of the building. And even though energy efficient appliances lessen energy use and our energy grid is getting cleaner through renewables, you can’t go back to replace the carbon that results from the current grid. So, there has been this shift in the industry towards contemplating going back to basics – dimensional stone, which means large blocks of stone.
Recently, in New York, organized by the Architectural League, a panel discussion called From Field to Form:Stone, which highlighted tensioning and using stone structurally. Unfortunately, I couldn’t attend. But, I spoke to my colleagues afterward, and we pondered the question together – why not dimensional stone? (Instead of crushing and processing stone to make concrete, just to reform into a cementitious form.)
After all, we are still enamored with stone. Look at Rex’s Perelman Performing Arts Center or the American Museum of Natural History Gilder Center Expansion by StudioGang Architects. We’re still hella into stone – there is romance in its unpredictability; we try to control which stone panel goes where to make sense of and to develop a pattern from stone’s natural and innate qualities such as veining and coloration. That’s the human in us, making sense of the earth, what it has to offer and beyond, much like how stargazing led to navigation.
While this variety in performance is the price to pay for this material’s beauty, as stone is a naturally occurring material, that’s part of the reason why traditional pre-industrial stone empirical construction had such wide stone walls – using extra material to account for the inconsistency of the material itself was an “easy” approach to take when there was so much left to the unknown. Science at its core is the identification and application of trends that result from doing the same thing over and over again, so that the results become predictable. (And, on the contrary, that adage of doing the same thing over and over again and expecting a different result is insanity. Maybe that is the joy and wisdom of mother nature – try as we might, there will always be some unknowns, and we should let that keep us humble.) And much like stargazing was the precursor to cosmology, advancements in mechanics of materials and materials science have enabled us to apply the scientific method to anticipate the strength of a stone, given ample specimens and repeated results from the same tests (breaking the stone repeatedly in specific and creative ways – think like Leonardo Da Vinci meets Mythbusters).
So, is there a future of using giant blocks of stone to build again? I’m not sure. But, for the sake of the earth, we have to confront our aesthetic leanings towards complex geometry and stone. Even the Guggenheim was originally conceived to have pink stone cladding over its now iconic concrete structure (that is blotchy due to issues in the finish consistency – Frank Lloyd Wright was livid that the stone was deleted due to cost and not pleased with the diagonals from the wood formwork, even ground down). Stay tuned for part two, when we take our critical looking glasses towards a new building. – KC
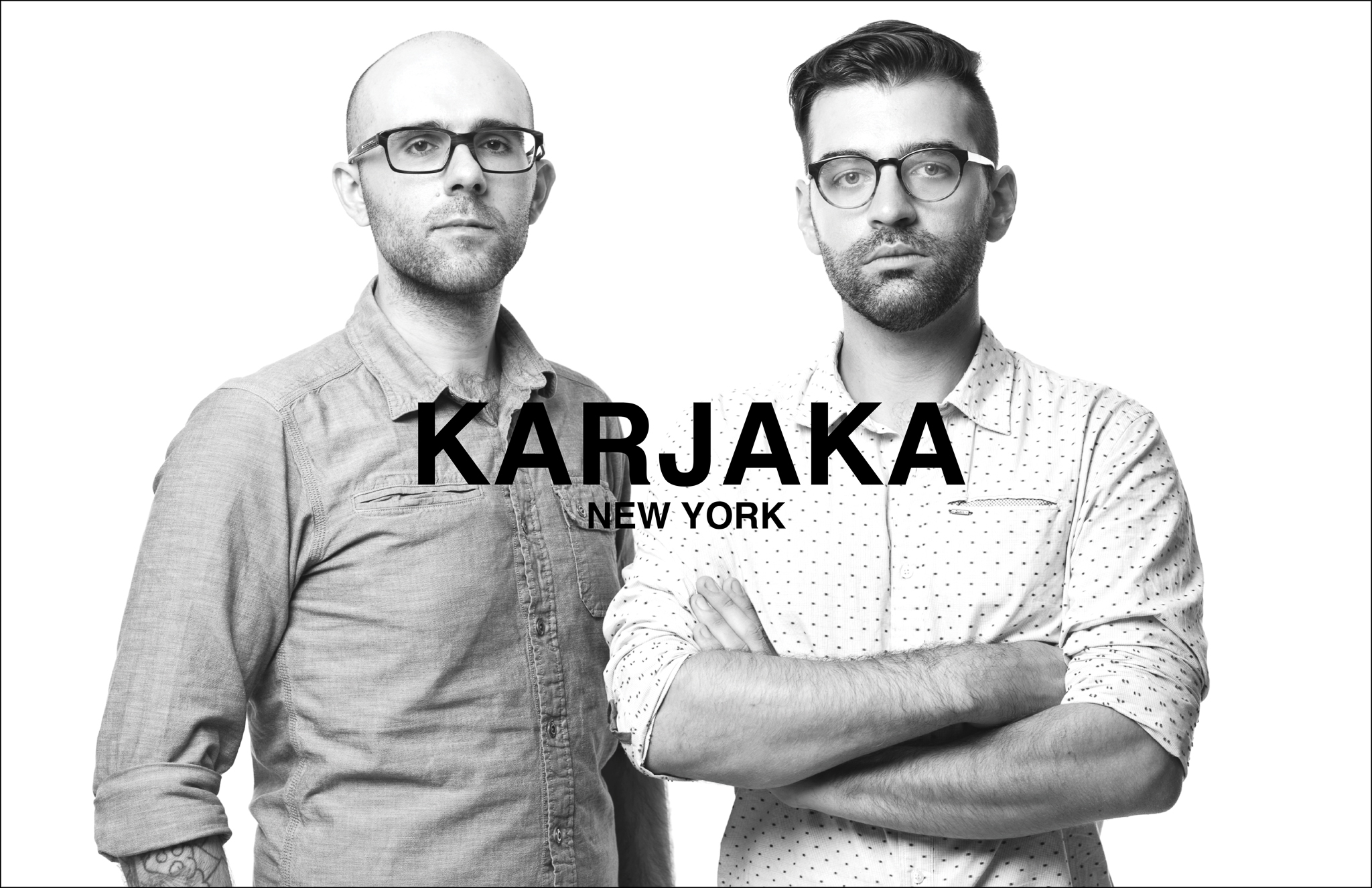